A properly designed control system with a well-programmed plc-program is very important in the strive for a smoothly running press with a short dead cycle time. Furthermore, it enables the use of synchronized control and a high level of reliability and repeatability. This gives a possibility to run the press very accurately and fast with small margins and yet with a very high level of safety.
HAX Technologies’ extrusion press program has been developed during many years focusing on performance and operator and maintenance usability.
HAX Technologies offers re-programming of existing programs, upgrades and complete installations of new systems. After completed installation our optimization team will tune the press to run smooth and with a minium dead cycle time.
Construction
We design control systems for both new and old machines. For electrical drawings we use the software EPLAN P8 and we have long experience in making special design control system for different kinds of machines with both hydraulics, pneumatics, servo control and variable frequency drives.
Modernization
The control systems develop rapidly and often become outdated and difficult to maintain long before the machine has served its useful life. When it comes to aluminum presses, it is not uncommon for the control system to be changed both two and three times during the life of the press. The biggest problems with older control systems are usually the availability of spare parts and expertise. So, why replace a working control system just because it’s a few years old? Is there good availability of spare parts and personnel who are used to handling the system and know what to do when something goes wrong. Then it might not be necessary. But if the parts have stopped being produced, the own warehouse is empty and you have to rely on the second-hand market in the event of a breakdown. Or the special programming cable that is needed is left behind in an electrical cabinet somewhere in the facility and in the computer with Windows XP, which is the only computer that has the right software to connect itself, the battery has long since collapsed. Then maybe it is high time to draw up a plan for modernization.
Today’s customers demand short lead times and small stocks. Then you cannot afford to stand still with the machine for an emergency replacement of control system parts. On the contrary – a good overview of the control system is a prerequisite for high availability over time!
Let’s take a look at your control system and we can jointly develop a plan for modernization.
Migration
We work with the most common control systems on the market, Siemens and Allen-Bradley. Both Allen-Bradley and Siemens have solutions for converting, for example, PLC5 to ControlLogix, SLC to CompactLogix or Siemens S5 to S7-1500. We have used both variants to make a modernization with minimal downtime in the machine and little work effort for re-wiring of cables.


Field busses
When you do a modernization, you usually take the opportunity to also upgrade the field bus. To make full use of a modern control system, fast response times and high transmission capacity are required. For Siemens we recommend a transition from Profibus to Profinet and for Allen-Bradley systems we recommend a phasing out of the older ControlNet and DeviceNet to Ethernet/IP. DH+ and RIO are also old bus types that have served their purpose.
HAX Technologies is a registered System Integrator at Bronze level for Rockwell Automation, meaning that we have acknowledged competence when it comes to Allen-Bradley control systems.
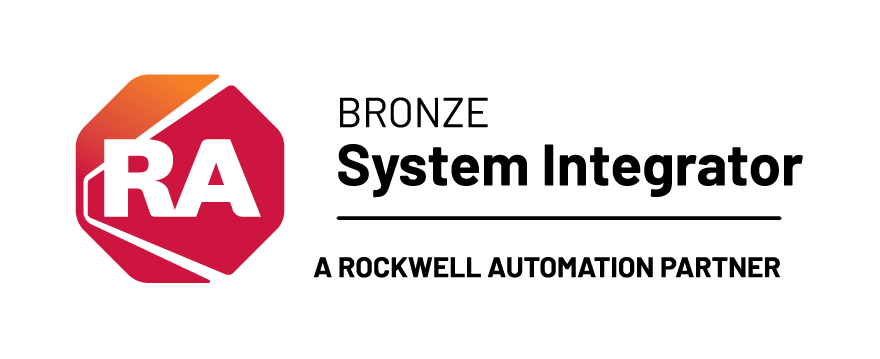